Die Casting: Precision and Durability
Die casting is a versatile and efficient manufacturing process used to produce high-precision metal parts with excellent surface finish and dimensional consistency. Utilizing high-pressure techniques to mold metals into complex shapes, our die casting services are ideal for creating durable components for automotive, consumer electronics, and industrial machinery.
Produces complex metal parts with tight tolerances and smooth surfaces.
Strength and Durability
Parts made through die casting are stronger than those made with other metal forming techniques due to the alloy’s excellent mechanical properties.
High Production Efficiency
Offers a fast cycle time per part, significantly reducing overall costs for high volume runs.
Versatility in Materials
Commonly uses alloys like aluminum, zinc, and magnesium, which are lightweight, durable, and suitable for a wide range of applications.
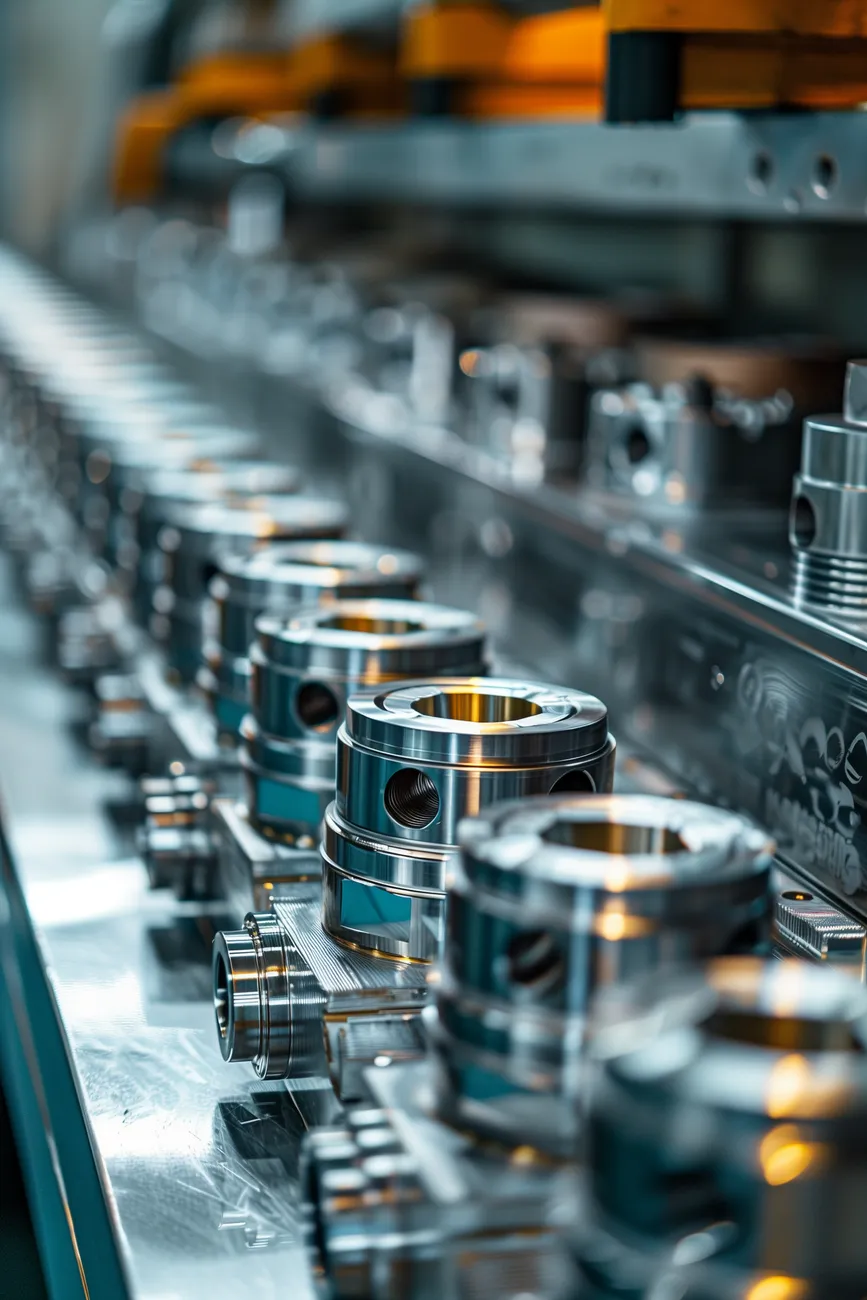
Die Casting Process
- Mold Design and Preparation: Starts with creating a high-strength steel mold capable of withstanding the high pressures of the die casting process.
- Molten Metal Injection: Metal is melted and injected into the mold under high pressure, quickly solidifying to form the part.
- Trimming and Finishing: Excess material is trimmed away, and secondary processes like drilling, machining, or surface finishing are applied to meet precise specifications.
Materials Commonly Used in Die Casting
- Aluminum: Offers a good balance of weight, strength, and thermal properties, ideal for automotive and aerospace components.
- Zinc: Known for its high ductility and impact strength, perfect for intricate designs.
- Magnesium: The lightest structural metal, used for ultra-lightweight and robust parts in mobile devices and automotive applications.
Why Choose Die Casting
Die casting is particularly advantageous for projects that require:
- High-Volume Manufacturing: Efficient for producing large quantities of parts due to low per-unit costs and fast production cycles.
- Consistent Quality for Complex Parts: Achieves high levels of detail and uniformity in parts, crucial for functional and aesthetic applications.
- Durable Metal Components: Produces parts that need to withstand rigorous use and environmental conditions.
Frequently Asked Questions About Die Casting
What is the maximum size of parts you can produce with die casting?
Our die casting capabilities allow us to produce parts up to 500mm in size. The maximum size can vary depending on the metal used and the complexity of the part, but we are equipped to handle large-scale components for various applications.
Can you produce parts with varying wall thicknesses?
Yes, die casting enables the production of parts with varying wall thicknesses. Optimal design ensures uniform cooling and solidification, which is crucial for maintaining structural integrity and achieving the desired mechanical properties.
What is the typical turnaround time for a die casting project?
The typical turnaround time for a die casting project ranges from 4 to 6 weeks. This includes mold design and fabrication, followed by the actual casting process. Timelines can vary based on the complexity of the mold and the finishing requirements of the final part.
How do you ensure the quality of die-cast parts?
We ensure the quality of die-cast parts through rigorous process control, starting with the design of the die to ensure proper filling and minimal defects. Each part undergoes strict inspections using dimensional checks, X-ray imaging, and mechanical testing to meet our high-quality standards.
What are the finishing options available for die-cast parts?
We offer a range of finishing options for die-cast parts including trimming, sanding, shot blasting, painting, powder coating, and anodizing. These finishes not only enhance the appearance but also improve corrosion resistance and surface durability, tailored to the specific needs of the application.
Get a Free Die Casting Quote
Tell us a bit about your needs and a knowledgeable product specialist will be in touch to gather any additional info and provide you with a secure file upload link to share your project files so we can get you an accurate quote.
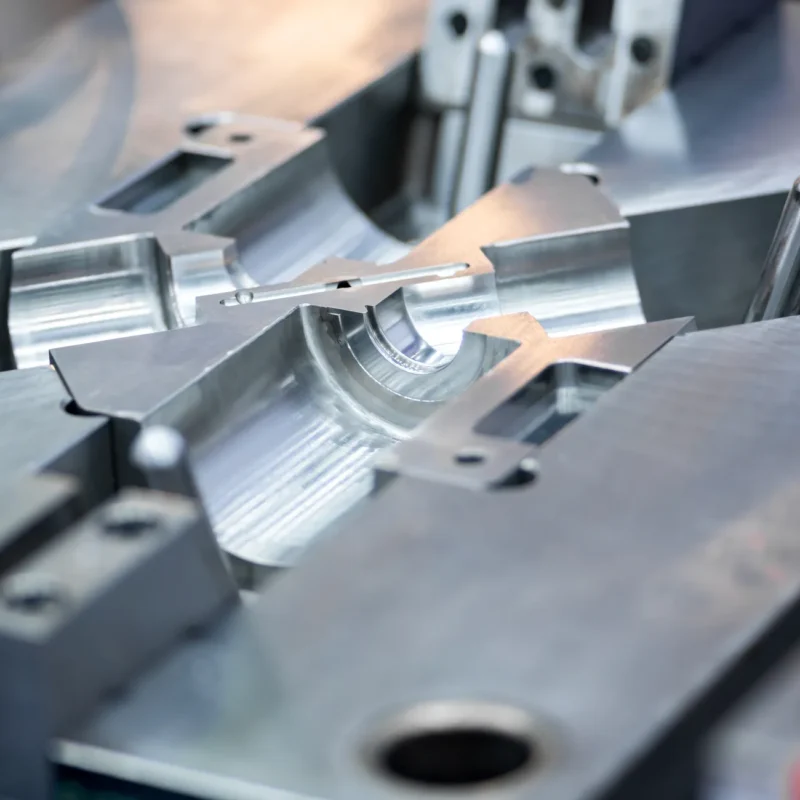